The first cameras used at RTVF were RCA TK-60 models. They employed a 4 1/2 inch Image Orthicon pick-up tube, and had 4 lenses mounted on a turret. One camera had a Varitol zoom lens. These cameras were built like tanks, and were introduced in 1962. The Image Orthicon tubes had their own “look” that included halos around bright objects, but when properly aligned, they could make nice looking black and white video. The photo below was taken “early-Bob Swanner.” but “post-flood”. Bob was instrumental in making physical upgrades to Tech Center, and one of these upgrades was the installation of a suspended ceiling…missing in this shot. But the photo also shows a 4 inch drain pipe installed in the ceiling. That puts the photo post-chiller-condenser rupture. (A future post will deal with Tech Center’s affinity for water).
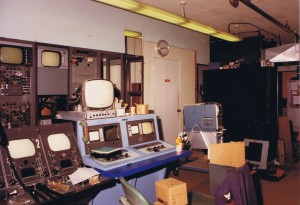
Tech Center before color cameras
Even though the TK-60s were monochrome and turret lens equipped, they did give the students the feel of trucking and dollying a professional-sized camera and pedestal. By the time we revived a full complement of cameras, we had them sitting on cam-heads which permitted students to experiment with tilt/pan drags and locks.
The TK-60s were a very important camera in the history of RCA broadcast cameras, and incorporated some RCA “advancements” such as Nuvistor tubes in the preamp, and an image orbiter to keep the Image Orthicon from burning-in. They were used world-wide.
There were quite a few TK 60 cameras locked away in the storage room. Apparently, WBAL in Baltimore had made some available to the department. Here’s a station-made camera logo plate (yes…TV stations once had people who did things such as cut stainless steel and build contraptions for various purposes on an as-needed basis.)
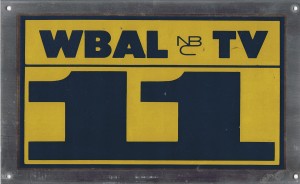
WBAL logo on a plate
Prior to the filming of the Barry Levinson film Diner, we were contacted by the production company and asked if they could rent the WBAL cameras for a scene that takes place in the WBAL studio. The rental never took place, but they did use the actual control room at WBAL.
On a non-RTVF note, I have a personal fascination with the use of TK-60s for “Electronovision”…a process by which live events were recorded direct to film using “high definition” TK-60 cameras. The French developed a monochrome video standard having 819 lines. I believe it was 25 frames per second. I have seen RCA equipment configured for 819 lines, and have to assume that Electronovision used cameras modified to run at 819/24 even though the spec sheet describes only 525/625 operation. (Have any Electronovision facts? Let me know). The TAMI show was recently released on DVD. If you want to see an important 60s Rock-and-Roll FILM shot with TK-60s, check out the link below.
The TAMI Show DVD
And if you are interested in the full specifications for a TK-60 camera chain, here is the 1964 RCA Broadcast Catalog layout. TK60 Technical Specifications
Oh, by the way. Check the TK-60 price on the last sheet of the tech specs. You could have purchased 5 Corvettes in 1964 for the price of one TK-60.